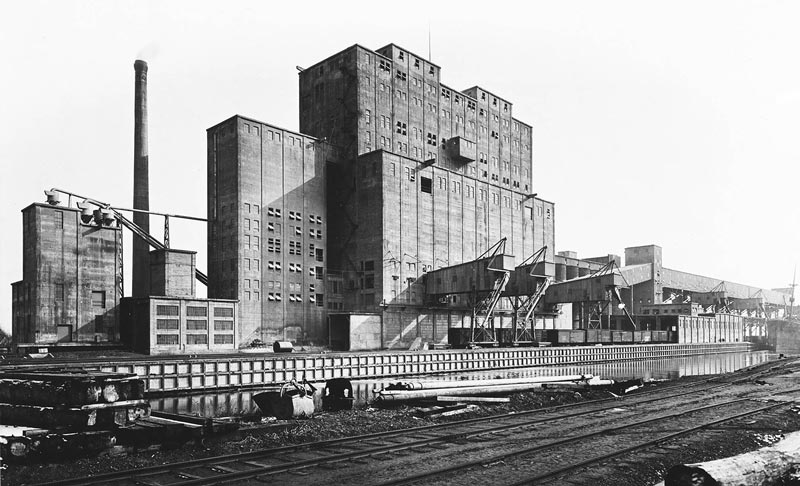
The Northern Central Grain Elevator of the Pennsylvania Railway at Canton, on the Baltimore waterfront. (Circa 1920)
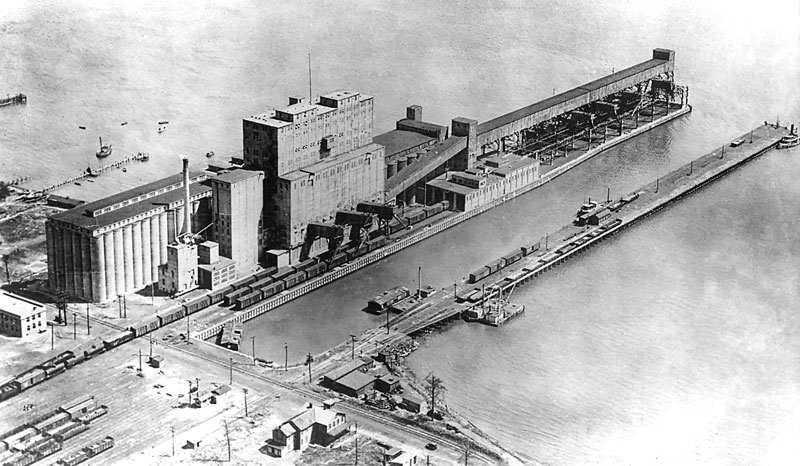
Successful Methods
August, 1920
More Than Modern
The Northern Central Elevator at Baltimore: A Structure That Is Ahead of the Times
By Jay Williams
Ordinarily, Successful Methods concerns itself with methods of construction. What happens to a structure after it is completed, how it is used, and the part it plays in the great field of industry, are usually matters in which this magazine's readers are not so keenly interested. But now and then the usefulness and success of a structure are so directly dependent upon the methods used in construction it, that a discussion of one leads into a discussion of the other.
The subject of this article, the Northern Central Grain Elevator of the Pennsylvania Railway at Canton, on the Baltimore waterfront, is a case in point. Any attempt to tell how it was built unfailingly leads into a description of what it does now that it is built, of the successful – and in many cases new – methods of grain handling which put it in a class by itself, several long jumps ahead of the time. To speak of it as thoroughly modern does not tell the story. The expression is inadequate. It is more than modern.
The northern Central Elevator is the larges on the Atlantic Coast. But that fact is relatively unimportant. Its quality is what makes it great, not its quantity. It was built by James Stewart & Co., under the direction of W. R. Sinks, manager of the Stewart organization's grain elevator department and work is still in progress on additional storage tanks which, when completed, will give it a total capacity of 5,000,000 bushels.
It is built almost entirely of concrete, and that is one of the points in which the methods of construction and successful operations are so entangled that they cannot be separated. A few words about the peculiar nature of grain elevators, and the ever-present dangers which attend their use, will explain the forgoing statement.
Handling grain is a dusty job, for, every time the grain is moved, a little more dust is shaken loose. And grain dust is dangerous; it explodes. Therefore, a method of construction which keeps the dust from finding lodgment here, there and everywhere, and reduces the danger of a disastrous explosion to a minimum is the most successful. That is where concrete scores. Its use makes it possible to build elevators with few ledges and sills. Few beams and other similar dust catchers. Steel frame elevators are still being built. But it only requires a brief glance into one of them and a look at the maze of beams and girders, with their convenient angles for dust collecting, to realize how good a piece of work the northern Central Elevator is. There the dust can collect only on the floor and almost nowhere else. Sweeping it up at frequent intervals is an easy task when it lies ready for the brooms instead of being hidden away in nooks and crannies ready to float forth and form part of a great explosion.
Placing the concrete at the northern Central Elevator involved some rather difficult feats. For example at one point it was necessary to shut the concrete about 720 feet. To do this the concrete had to be carried to the top of one tower, chuted to the base of another, and then delivered through a long chute suspended over the water.
Such methods as that just described made the work of construction a success, Now come the turn of the methods which are making the operation of the elevator a success. First and foremost are the four great car unloaders, mechanical monsters of a new species, the like of which never before has been seen. They pick up a box car almost bursting with its load of grain, tip it this way and that while the grain rushes out with a roar like a waterfall, and in less time than it takes to write about it, restore the car to an upright position all safe and sound, and after pushing it along, are read for the next one.
In language a little more technical, the work of the unloaders may be stated as follows: The car is run upon the unloader. When the operator in the cage overhead give the “go ahead” signal, he starts a motor which causes two clamps to rise from between the rails and press tight against the couplers at both ends of the car. The next move is to operate two side supports which press agains the sides of the car a few feet from the ends. When these are in place the car is tipped sideways to an angle of 30º, while at the same time a mechanical door opener is pressed agains the grain door, which is pushed inside the car as it tips. The pushing in of the grain door, which remains intact, releases the grain which begins to pour into the hopper beneath. To accelerate the flow, the car, still inclined sideways at an angle of 30º, is tipped endways as well, to an angle of 45º, if necessary. It is then tipped endways in the other direction, the grain rushing out first from one end and then from the other. When the grain has run out, the little which is left is cleaned out with an air hose while the car is being brought back to its original position. The car is then released and pushed out by the next car, as the latter takes its place on the platform on the unloader.
“Does such a big machine pay?” is a question that has been asked more than once by those ho have had the opportunity to see it since it was put to work only a month ago. Here are some facts and figures which answer conclusively the question with which this paragraph begins.
There are 4 unloaders at Baltimore, and at the present it takes three men to handle one. Although ultimately the number may be cut to two. That makes 12 men to operate 4 unloaders and at a normal speed it is easily possible to unload 240 cars in an 8 hour day. The whole operation of unloading a car has been performed repeatedly in 7 minutes.
Another big grain endeavor in this county employes 88 men working with the old-fashioned, but up till now, modern, grain car shovels, which are operated by a clever device which pulls the shovel through the grain to the door of the car. These 88 men, by working all day, can unload almost as many cars as the 4 unloaders operated by a dozen men. Does that answer the question, in these days of high-priced labor?
There is another item, too that was all but forgotten. At present prices it cost about $11 to cooper a grain car, that is, to put up the grain doors inside the regular door. The popular method of getting them out of the way is to take an axe and crow bar and chop them away, regardless of the cost. As a matter of fact, there was no other effectual way of releasing the grain. But the unloaders have put an end to that sort of wanton waste, so far as the norther Central Elevator is concerned. They pick up the grain door intact, hold it until all the grain has run out, and then deposit it, as good as ever, on the floor of the car. There is a practical dollars and cents savings that anyone can see and understand.
But the car unloader is only one of a number of refinements in methods of operation at the Northern Central Elevator. The other are less spectacular, but, nevertheless, do their share to make the handling of the grain as efficient and inexpensive as is humanly possible. The easiest way to tell about them is to follow the grain from the cars up through the “house” into the storage bins, and from there into the ships that take it across the Atlantic. Like all the other elevators on the seaboard, the Northern Central exists for the purpose of transferring grain from car to ship and for storing it while awaiting vessels to take it away.
From the hoppers into which the grain is dumped by the car unloaders, it is carried on the belt conveyors to the boot of the leg, which is the technical term for the elevating mechanism consisting of buckets on an endless belt. The legs - there are 19 of them, each 220 ft. in height - take the grain up to the garners in the top of the house. In most elevators the legs are driven by a rather complicated rope drive which takes up considerable valuable space, and requires the installation of special devices to keep the ropes a the right length despite the changing conditions. At Baltimore, the belts are driven directly by individual motors and also are equipped with automatic takeups and stops. These are real factors in the elevator's safety system, because, in the past, many explosions have been cause by the choking of the legs, with a resulting generation of heat by the revolving drive mechanism That cannot happen in Baltimore. The moment a leg chokes, the automatic stop does its bit, and everything come to a standstill.
To return to the grain. The garners, into which it is discharged by the legs, are bins which hold the grain from one car while that from the previous cars is being weighed. In a grain elevator every bushel is weighed, the superintendent is like a banker, and at the end of the year every bushel taken in must be accounted for, either as paid our or still held in storage. Therefore. It is necessary to keep the various carloads separate until they have been weighed.
The big scales, and there are 23 of them, weigh the grain at the rate of 2,000 bushels at a time. A signal system of lights operated by the grain dispatcher from his office where he can tell at a glance what every unloader, conveyor, leg, scale or spout in the elevator is doing, as well as the conditions of the storage bins, tell the weigher when and where to discharge the grain from his scale. It may be sent to one of three places: into the storage bins, directly into the ship, if one is waiting, or back to the cars. That is up to the grain dispatcher, who governs his actions by the needs of the moment.
If it is sent to storage, the grain is discharged by spouts to the belt conveyors which carry it to any one of the storage bins, or tanks. There are two kinds of storage bins: the big, circular ones which hold 13,000 bushels each, and the interstitial bins which very cleverly utilize the spaces between the round tanks. Storage space is not wasted in a modern grain elevator.
In order to withstand the lateral pressure, the tanks are built of concrete in circular form, reinforced by steel rings, like hoops on a barrel. As wheat weighs about 50 lb. to the cubic foot, as opposed to about 62 lb. for water, the necessity for strength can be understood easily.
So much for the big storage tanks. It frequently happens that the grain, after being weighed, is not put in storage, but is sent directly to the ships. In such cases it is discharged from the scales into the shipping bins and from them into the discharging spouts. In the construction of this spouting system, the elimination of dust was kept in mind. The spouts are all encased, and hoppers are provided which break the fall of the grain half way down, thus reducing greatly the amount of dust. Gravity and belt conveyors attend to the task of getting the grain into the ship.
The drying house has not been mentioned in the forging chronicles of the progress of the grain through the elevator because it isn't always needed. Some grain behaves so well that it doesn't need a trip the dryer. A separate building handles this department, in which the grain is sifted through bins so constructed that both hot and cold air can be blown through it. At any time grain can be taken from the storage tanks, dried or cleaned, and then returned to the tanks or went to a ship.
That about covers the high spots, and there isn't space enough for a detailed description of all the many ways in which safety, efficiency and economy are obtained at the Northern Central Elevator. There is one thing more, however, that must be mentioned. That is the fire alarm system. Even though everything possible had been done to prevent fire, the builders didn't overlook the necessity of getting right after it, if it should break out. The telephone system is the fire alarm system, and the fire signal is 00. That doesn't mean that you have to call up a central operator to report a fire. Nothing as crude as that. You just take down the receiver, call 00, and the fire pump starts, the alarm rings and the fire fighting forces go into action. Simplicity and safety again - the twin virtues that keep cropping up throughout the mighty establishment.
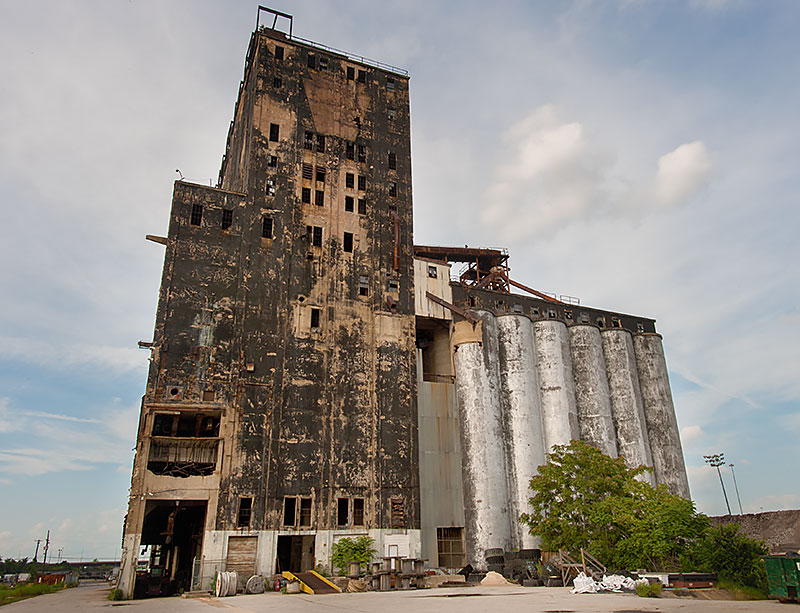
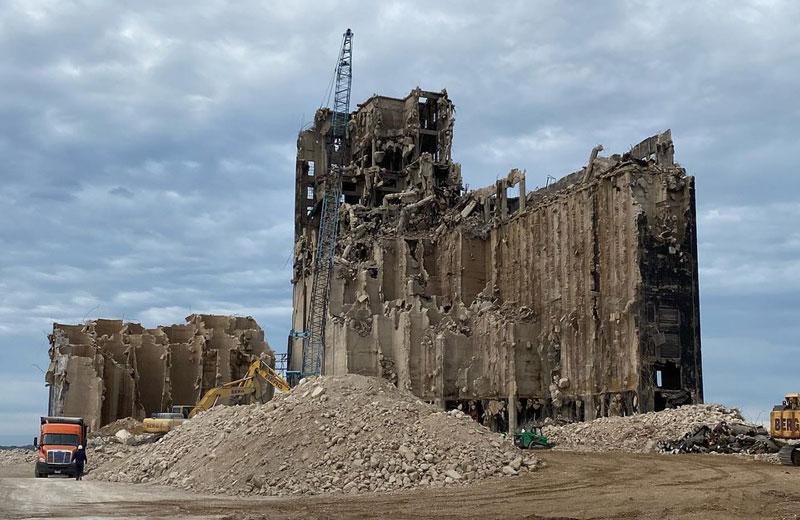